Sika® WT-200 P
Sika® WT-200 P is a combined water resisting and crystalline waterproofing admixture used to reduce the permeability of concrete and to enhance the self-healing abilities of the concrete.
Sika® WT-200 P has the following characteristics and benefits:
- Reduced water penetration under pressure
- Reduced water absorption
- Enhancement of self-healing properties of the concrete
- Improvement in resistance against chemical attack
- Reduced vapour transmission
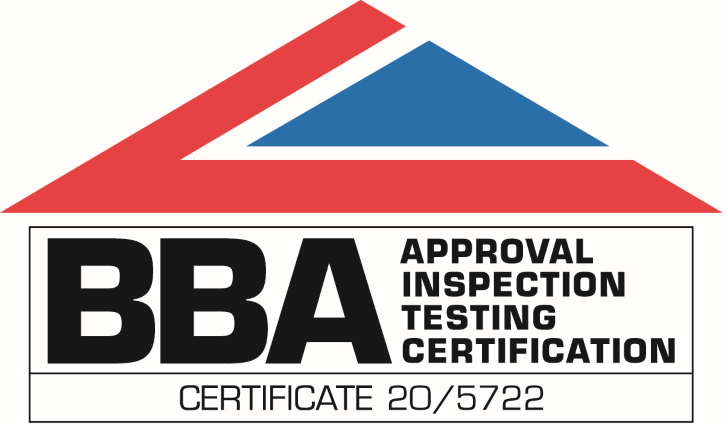
For this content to be displayed, you need to accept all cookies in the cookie settings and confirm your selection or by clicking the “Allow All” button.
Usage
Sika® WT-200 P has been specifically formulated to produce high quality waterproof concrete. Sika® WT-200 P treated concrete is used as a part of the Sika® Watertight Concrete System.Sika® WT-200 P can be used in any watertight structures such as:
- Basements
- Parking garages
- Utility / plant rooms
- Tunnels
- Swimming pools
- Water retaining structures
- Dams
- Waste water treatment structures
- Underground commercial facilities (malls, transportation hubs etc.)
Advantages
Sika® WT-200 P consists of a mixture of active materials which form non-soluble products throughout the pore and capillary structure of the concrete and seal the concrete permanently against the ingress of water and other liquids. In addition, the special formula and ingredients of Sika® WT-200 P enhances the self-healing properties of concrete and will improve the ability to heal cracks.Sika® WT-200 P has the following characteristics and benefits:
- Reduced water penetration under pressure
- Reduced water absorption
- Enhancement of self-healing properties of the concrete
- Improvement in resistance against chemical attack
- Reduced vapour transmission
Packaging
1.75 kg soluble bags
Colour
Grey powder with some small agglomerations
Product Details
APPROVALS / STANDARDS
- Conforms to the requirements of BS EN 934-2 Table 9
- DoP 84924988, certified by Factory Production Control Body 1029 and provided with the CE mark
- DoC 22515203, certified by Factory Production Control Body 0120 and provided with the UKCA mark
- BBA Agrément Certificate 20/5722
Chemical Base
Mixture of cements, amino alcohols and fillers
Shelf Life
12 months from date of production if stored in unopened and undamaged original sealed containers.
Storage Conditions
Storage at temperatures between 5 °C and 30 °C. Protect from direct sunlight, moisture, frost and contamination.
Bulk Density
~750 kg/m³
pH-Value
~12 (dispersed in water)
Total Chloride Ion Content
<0.1 % w/w (chloride free)
Equivalent Sodium Oxide
<4.0 % w/w (alkali content)
Concreting guidance
The standard rules of good concreting practice, concerning production and placing, are to be followed.
Laboratory trials shall be carried out before concreting on site, especially when using a new mix design or producing new concrete components.
Fresh concrete must be cured properly and curing applied as early as possible.
Specific Advice
Due to the production process, some small agglomerations or lumps of powder may be visible in the bags, but these will break down in the mixing process. These should be able to be easily broken up by hand.
Concrete Mix Design
- For waterproof concrete: Concrete mix design depends on local requirements and / or local standards for watertight concrete systems.
- For Sika® Watertight Concrete: Sika® WT-200 P has been formulated for use in concrete with a minimum binder content of 350 kg/m³ and a maximum w/b-ratio of 0.45. Depending on the specific mix design the dosage of HRWR/superplasticizer has to be evaluated in order to achieve a S3 / F4 consistence class (EN 206-1).
- Laboratory trials are always recommended to evaluate and confirm actual water reduction and consistence class.
Effect on Setting
The chemical and physical composition of the components, concrete, Sika® WT-200 P and concrete and ambient temperature can affect the setting time of the concrete.
Application
Dispensing
- Forced action and truck mixers should be free from all contaminants prior to the batching of concrete containing Sika® WT-200 P.
- Sika® WT-200 P should be added to the mixer at the recommended dose (2 bags per m3) prior to the batching of concrete.
- Batched concrete mix constituents should be subsequently batched on to the Sika® WT-200 PP in accordance with Sika® mix design recommendations.
- Additional mixing water should then be dispensed to bring the concrete to the desired consistence.
- On completion of the batching procedure the concrete load should be mixed in the truck mixer/agitator on full revolutions for a minimum of 5 minutes to ensure that the optimum consistence has been achieved.
- The w/c ratio and consistence control remains the responsibility of the concrete producer. Laboratory trials are recommended to evaluate and confirm the actual water reduction.
Compatibility
Sika® WT-200 P may be combined with many other Sika products.
Always conduct trials before combining products in specific mixes and contact Sika technical service for more information and advice.
Recommended Dosage
2 x 1.75kg bags of Sika® WT-200 P per m3
FAQ
Any cost differential depends on several factors, such as:
- Thickness of concrete section.
- Location of site.
- Size of project.
- Access limitations.
- Build schedule of project.
- Joint Sealing
The cost of repairing a leaking basement, which didn't have adequate waterproofing measures at design stage, is usually many times more expensive than making the structure watertight at the start.
BS 8102:2022 Code of Practice for Protection of below ground structures against water ingress.
Drying is the escape of moisture from the concrete element. The rate of evaporation from the watertight concrete surface is slightly slower than conventional concrete due to its higher density and action of the admixtures themselves. It will be greatly affected by factors such as mix design, temperature, ventilation and curing regime. Depending on the requirements of any coatings to be applied to the surface, different levels of moisture may be acceptable.
Curing is the chemical reaction between cement and water which generates strength and density within the concrete. The curing time of WTC will be similar to plain concrete and should not affect time required to strike formwork, for example. Factors such as cement content, temperature and cement type will have a much greater influence on this aspect.
If the project requires a Sika guarantee, then site visits by Sikae technicians are required and supplied free of charge. Otherwise, site support would be on a project-by-project basis.
Movement joints must be sealed with either a suitable internal or external waterbar or post-applied flexible strip (Sikadur Combiflex). These allow for differential movement of the adjacent concrete components. Please contact Sika for information on movement joint solutions to ensure the correct one is specified.
In general, the minimum section thickness is 175 mm but aim for 200 mm minimum section thickness to allow for tolerance in waterbar placement location.
A pour schedule with joint locations would be normally agreed by the structural engineer and Sika's technical department prior to placing the concrete.
- For vertical watertight concrete, walls should be poured in sections with a maximum aspect ratio (length to height) of 3:1, ending in a construction / day joint, but precise joint locations should be decided by the structural engineer. Dwarf walls with a height of <1 m may be extended to a 5:1 aspect ratio.
- For horizontal watertight concrete slabs, the maximum area without a construction / day joint should in general be 400 m2, assuming the slab shape is close to 1:1 aspect ratio, but precise joint locations should be agreed with the structural engineer.
- For capping beams, precise joint locations should be decided by the structural engineer in agreement with Sika’s technical department.
Where watertight concrete may be more expensive per/m3 than standard concrete, a membrane will come with an added cost of labour and time in the programme. In most situations reinforced concrete already forms part of the structure, so there is minimal extra labour and construction time required to incorporate watertight concrete admixture.
Please note that for a grade 3 structure, two forms of protection are often required and all projects should be viewed on their own merits based on risk, required internal environment and construction types and limitation.
In addition, when working alongside major warranty providers (NHBC etc), there maybe a requirement to use two forms of waterproofing to provide adequate protection.
Mix designs are produced by the ready-mixed concrete supplier then checked and approved by the Sika Technical Services team.
Sika offers a 15 year guarantee for Sika Watertight Concrete system, including joint sealing. This increases to 20 years for certain dual waterproofing systems, where a type A or type C waterproofing solutions are installed in combination with the Sika Watertight Concrete or 25 years where three types are used.
Yes, we have a full suite of standard details for all waterproof systems, also available on our waterproofing website.
Not as a standalone system but it can form part of a gas-resistant waterproofing specification incorporating a suitable gas barrier such as SikaProof or Sikaplan membranes. Overall basement ventilation should be considered, for example in basement car parks, the building may already have appropriate ventilation due to the layout of access ramps for cars whereas a habitable basement may require a forced ventilation system.
Yes, generally a liquid admixture (Sika-1+) works best through this type of mixer to allow constant feed during production. Concrete producers operating volumetric trucks should have third party quality accreditation and current calibration certificates for all their vehicles. If a Sika Guarantee is required, an audit of the quality procedures by Sika’s Technical Department will be required prior to starting the project.
1. A Sika Specification document for the project must be issued by a Sika Specification Manager.
2. A Sika tool-box talk is given to the installing operatives prior to commencement on site.
3. A Sika Technician has performed at least one interim site visit.
4. Any actions and non-conformities identified in the Site Attendance Log have been completed to Sika’s satisfaction.
5. A Final Assessment has been completed prior to commencing internal works, i.e. plastering or covering over the concrete. The areas must be clear, dry and accessible for the Final Assessment.
6. Complete and return the Sika Application for Waterproofing Guarantee form.
The Final Assessment must be carried out with no exceptions. It is the installing contractor’s responsibility to inform Sika they are ready for the assessment. All Sika waterproofing materials must be or have been available for visual check, this includes any repairs carried out by either the Contractor, Sika Limited, or their appointed specialist contractor.
Any areas of waterproofing that were / are not available for assessment may be excluded from any guarantee. When all parties are satisfied that a successful job has been achieved, the Sika Application for Waterproofing Guarantee form must be completed by the installing contractor and returned to Sika within 12 months of final assessment.
Both are covered by the same Sika guarantee.
- In areas of constant water pressure against the structure, this will fully utilise the crystallising effects of WT-200 P.
- In areas with variable water table, pore blocker may be the preferred option.
There are many types of joint sealing solutions depending on the application and conditions. Generally, for construction joints Hydrophilic Strips (SikaSwell) are popular, but coated metal strips (Sika Metalsheet FBV), Injection hoses (SikaFuko) or PVC Waterbars can also be used as part of the system. All are compatible with watertight concrete and at least one Sika joint protection system should be used in a continuous network in order to receive the Sika Guarantee.
9 metres in most situations, but precise joint locations should be decided by the structural engineer in agreement with Sika’s technical department. Joint sealing details should be agreed between pours.
The structural concrete element is to be designed in accordance with the flexural and thermal crack limitations stated in the relevant sections of BS EN 1992 Eurocode 2, with maximum crack widths of 0.3 mm or 0.2 mm, depending on design criteria and application, and as stated in relevant product BBA Certification.
Yes, whichever admixture is chosen, it works as part of a system where joint protection and good site practice are equally important to deliver a watertight structure.