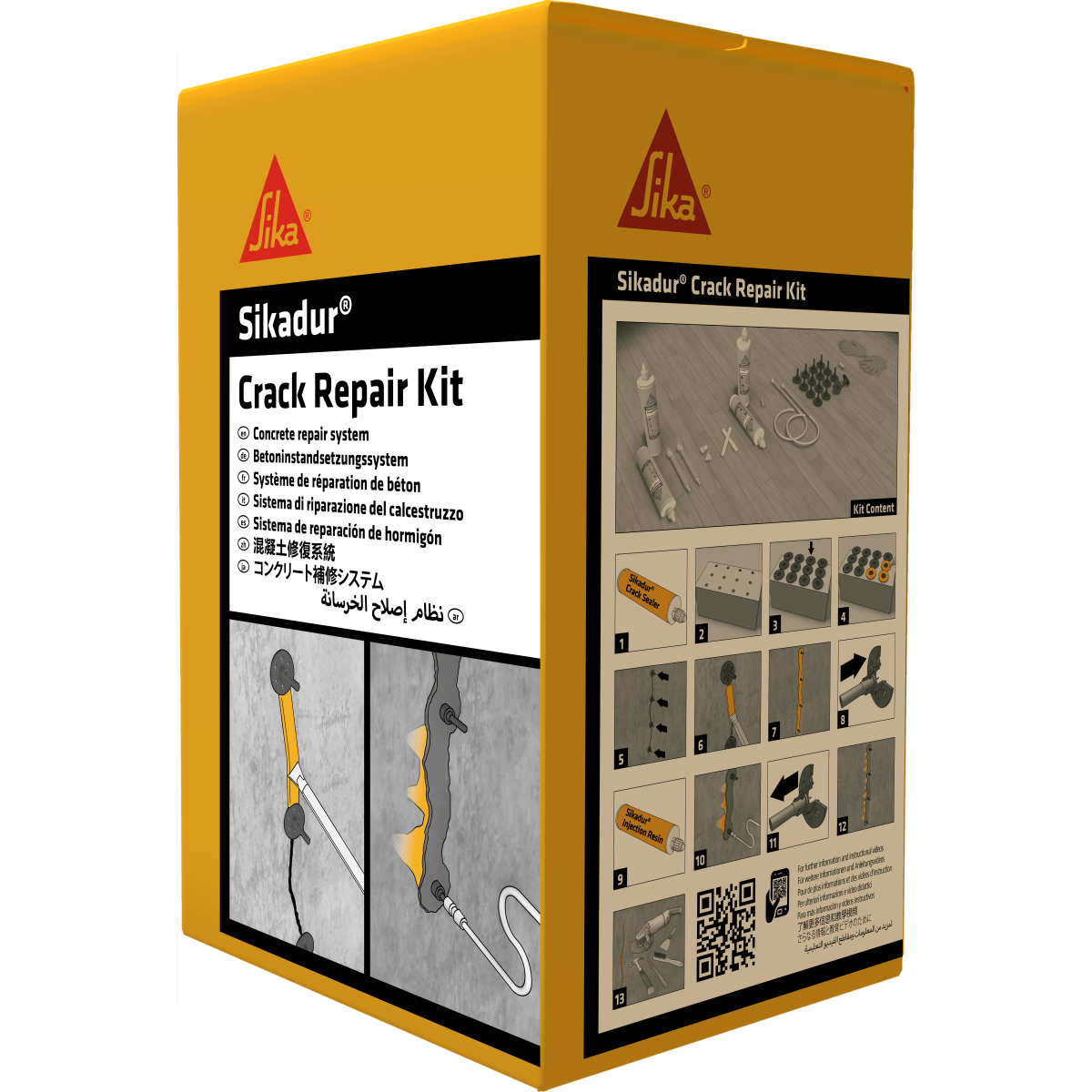
Sikadur® Crack Repair Kit
Sikadur® Crack Repair Kit is for repairing and sealing of small / minor cracks in concrete and masonry. It includes a two-part polyester surface crack sealer, two-part low viscosity epoxy injection resin and all the necessary accessories needed for the application.
- Full kit, including all necessary accessories for carrying out complete application.
- Easy application using cartridges that fit standard cartridge application guns.
- Fast curing surface crack sealer and injection resin.
- Low viscosity for deep penetration into cracks.
- Convenient 'mix in the nozzle' cartridge system.
Usage
Repairing and / or sealing cracks in concrete and solid masonry using:- Low pressure resin injection technique for vertical, horizontal or overhead applications.
- Gravity feed technique for horizontal applications.
Advantages
- Full kit, including all necessary accessories for carrying out complete application.
- Easy application using cartridges that fit standard cartridge application guns.
- Fast curing surface crack sealer and injection resin.
- Low viscosity for deep penetration into cracks.
- Convenient 'mix in the nozzle' cartridge system.
Packaging
Kit contents:
- Sikadur® Crack Sealer 300 ml cartridge (2 pcs)
- Sikadur® Injection Resin 250 ml cartridge (2 pcs)
- Sikadur® Crack Sealer mixer nozzle (2 pcs)
- Sikadur® Crack Sealer applicator fan (2 pcs)
- Cartridge flow restrictor (2 pcs)
- Sikadur® Injection Resin mixer nozzle with extended tube (2 pcs)
- Push fit connector (1 pc)
- Injection ports (16 pcs)
- Pair of gloves (2 pcs)
- Wooden applicator (Spatula) (2 pcs)
Colour
Sikadur® Crack Sealer (Parts A+B mixed) | Concrete grey |
Sikadur® Injection Resin (Parts A+B mixed) | Transparent / Yellowish |
Product Details
APPROVALS / STANDARDS
- CE Marking and Declaration of Performance to EN 1504-5 - Concrete injection.
- Conforms to ASTM C-881 Grade 1, Class C, Types I, II.
Shelf Life
18 months from date of production.
Storage Conditions
The product must be stored in original, unopened and undamaged packaging in dry conditions at temperatures between +5 °C and +25 °C. Always refer to packaging.
Density
Sikadur® Crack Sealer (A+B mixed) | ~1,6 kg/l |
Sikadur® Injection Resin (A+B mixed) | ~1,1 kg/l |
Viscosity
Sikadur® Injection Resin (A+B mixed) | ~500 cps at +23 °C |
Volatile organic compound (VOC) content
Sikadur® Crack Sealer | 4,3 % |
Sikadur® Injection Resin | 5,4 % |
Compressive Strength
Sikadur® Injection Resin
Time | Temperature | ||
+5 °C | +20 °C | +35 °C | |
4 hours | - | - | ~4 N/mm2 |
8 hours | - | - | ~16 N/mm2 |
16 hours | - | ~17 N/mm2 | ~25 N/mm2 |
1 day | - | ~24 N/mm2 | ~37 N/mm2 |
3 days | ~11 N/mm2 | ~62 N/mm2 | ~39 N/mm2 |
7 days | ~46 N/mm2 | ~65 N/mm2 | ~49 N/mm2 |
14 days | ~55 N/mm2 | ~67 N/mm2 | ~55 N/mm2 |
28 days | ~65 N/mm2 | ~70 N/mm2 | ~70 N/mm2 |
Product cured and tested at temperatures indicated in table. Test specimen size: 12,7 mm × 12,7 mm × 25,4 mm.
Modulus of Elasticity in Compression
~16,900 N/mm2 (7 days / +23 °C) | (ASTM D 695) |
Flexural Strength
~70 N/mm2 (7 days / +23 °C) | (ASTM D 732) |
Tensile Strength
~43 N/mm2 (7 days / +23 °C) | (ASTM D 638) |
Tensile adhesion strength
Dry concrete | > 3,2 N/mm2 (concrete failure) |
Moist concrete | > 2,0 N/mm2 (concrete failure) |
All values determined after 7 days at +23 °C.
Heat deflection temperature
~43 °C (~110 ° F) (7 days / +23 °C) | (ASTM D 648) |
Water Absorption
~0,24 % (7 days / +23 °C) | (ASTM D 570) |
Application
Mixing Ratio
Sikadur® Crack Sealer | Part A : Part B = 10:1 |
Sikadur® Injection Resin | Part A : Part B = 1:1 |
Layer Thickness
Sikadur® Crack Sealer | Maximum ~8 mm |
Sikadur® Injection Resin | 0,1 – 6 mm |
Sag Flow
Sikadur® Crack Sealer (A+B mixed) | Non-sag, including overhead |
Sikadur® Injection Resin (A+B mixed) | Liquid |
Product Temperature
+5 °C minimum / +30 °C maximum
Ambient Air Temperature
+5 °C minimum / +45 °C maximum
Dew Point
Beware of condensation.
Substrate temperature during application must be at least +3 °C above dew point.
Substrate Temperature
+5 °C minimum / +45 °C maximum
Curing Time
Sikadur® Crack Sealer
Temperature | Open Time - Tgel | Curing Time - Tcur (Injection Time) |
+30 °C (86 °F) | 4 minutes | 30 minutes |
+25 °C (77 °F) | 5 minutes | 40 minutes |
+20 °C (68 °F) | 6 minutes | 50 minutes |
+10 °C (50 °F) | 10 minutes | 85 minutes |
+5 °C (41 °F) | 18 minutes | 145 minutes |
Sikadur® Injection Resin
Temperature | Open Time - Tgel | Peel-off Time (Crack sealer removal) | Curing Time - Tcur |
+30 °C (86 °F) | 20 minutes | 3 hours | 12 hours |
+20 °C (68 °F) | 30 minutes | 6 hours | 24 hours |
+5 °C (41 °F) | 2 hours | 18 hours | 72 hours |
Consumption
Depending on crack width and crack depth, the kit yields approximately 2-4 metres of crack length.
SUBSTRATE QUALITY
- Concrete must be at least 21 – 28 days old, depending on curing and drying conditions.
- Substrate surfaces along the line of the crack required for the Sikadur® Crack Sealer, must be sound, clean and dry. Free from standing water, ice, dirt, oil, grease, coatings, laitance, efflorescence, old surface treatments, all loose particles and any other surface contaminants that could affect adhesion of the injection ports.
- Cracks must be clean. Horizontal cracks, which are filled by the 'gravity feed' technique, should be v-notched along the entire crack length with grinding equipment.
MIXING
Preparing the Sikadur® Crack Sealer Cartridge
| 1. Unscrew and remove the cap. |
| 2. Cut the end off the protective film. |
| 3. Screw on the square mixing nozzle. |
| 4. Place the cartridge into the application gun ready for use. Pump gun until both resin parts are extruded as one mixed consistent colour. Do not use unmixed material. |
| 5. After bonding on the injection ports, remove the tip from the static mixing nozzle. |
| 6. Fit the applicator fan onto the square mixing nozzle then start the crack sealing application. |
Note: When the work is interrupted, the square mixing nozzle can remain on the cartridge after the gun pressure has been released. If the resin has hardened in the nozzle when work is resumed, a new square mixing nozzle must be attached.
Preparing the Sikadur® Injection Resin Cartridge
| 1. Unscrew the screwcap (do not throw away) and remove the plug from the cartridge outlet. |
| 2. Fit the cartridge outlet plug into the cartridge then place injection resin mixer nozzle onto the cartridge. |
| 3. Slide the screwcap over the injection resin mixer nozzle and screw onto the cartridge. |
| 4. Place the Sikadur® Injection Resin cartridge into the application gun ready for use. |
| 5. Fit the flexible extension hose onto the injection resin mixer nozzle. |
| 6. Fit push fit connector onto the hose. Pump gun until both resin parts are extruded as one mixed consistent colour. Do not use unmixed material. Place connector over an injection port and start the injection application. |
CLEANING OF TOOLS
Clean all tools and application equipment with Sika® Thinner C immediately after use. Hardened material can only be removed mechanically.